Tesla Model S
Tidbits Inside the Tesla Factory Tour in Fremont, CA
Last week, Michael Brown got his wish, a full Tesla factory tour. Later, he made a video of his thoughts from the experience and posted it to YouTube.
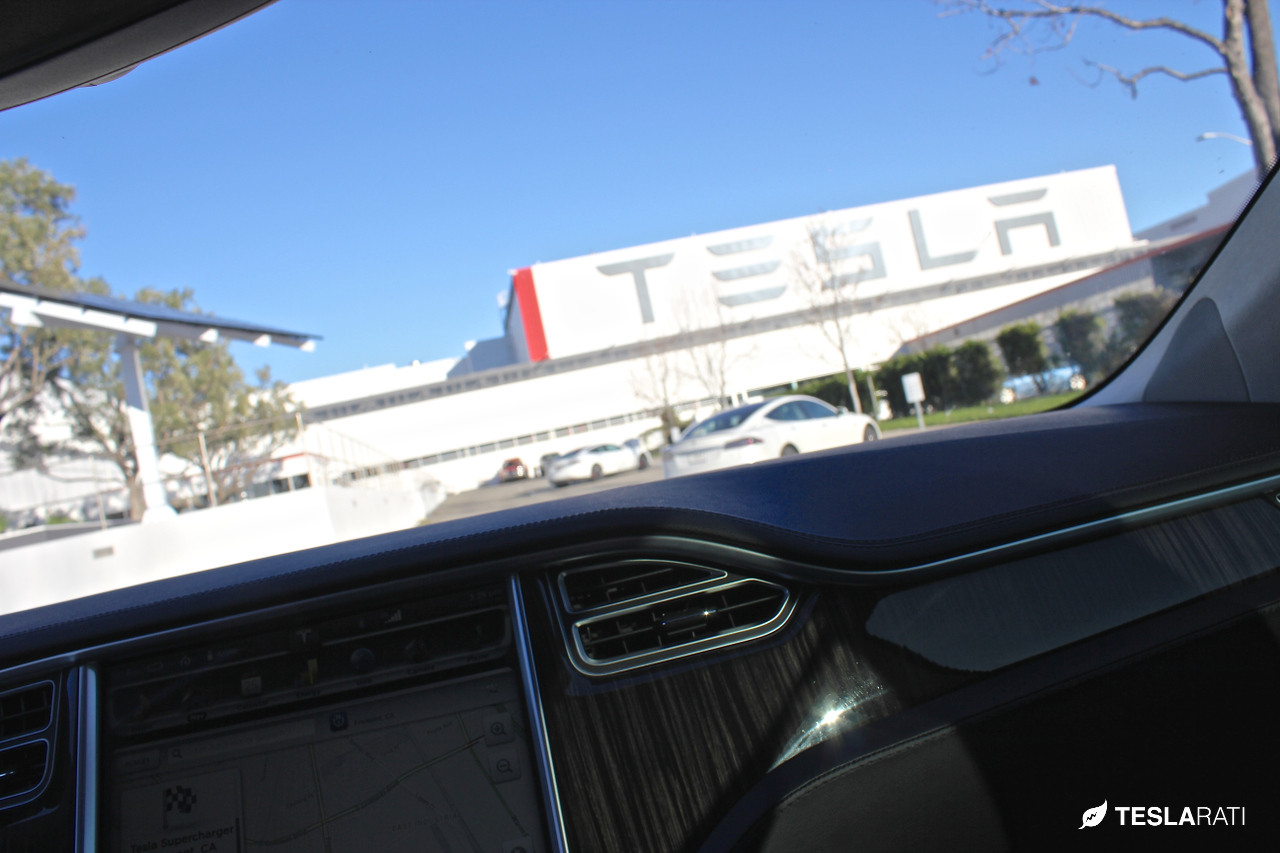
The morning after Elon made his debut on Stephen Colbert’s Late Show, one Tesla enthusiast got his wish by taking a Tesla factory tour which included a big bonus in the form of a Model X.
Michael Brown accounts what he saw during the Tesla factory tour on his YouTube channel.
According to Michael:
The tour started with a walk through of the enormous administrative and engineering departments just outside the production area. Program Manager of the Tesla Factory Tour, Adam Slusser, introduced the tour group to the rolled sheet aluminum and ingots from which the body of the car and its components are made. He learned that the total weight of the aluminum Model S chassis is only 410 lbs.
What amazed Michael is the bounty of production equipment left behind by Toyota after the Fremont factory was closed. Tesla bid on the empty factory building itself, but was surprised to learn that millions of dollars of equipment was being left behind and could be purchased for pennies on the dollar, including the largest stamping machine in North America valued at $72,000,000. It is driven by an 8,000 hp hydraulic pump and is 7 stories high — 3 underground and 4 above. The first time Tesla started it up, it triggered seismic warnings in Berkeley, 30 miles away.
The stamping line begins with 6 foot wide rolls of aluminum weighing 20,000 pounds each. Each piece takes 3-5 stamps to get it into the proper shape. A run of 600 pieces (enough for 600 cars) takes 2 days to complete. The factory floor utilizes more than 1,000 6 axis robots that are accurate to within 0.25 mm. The flexibility of these robots means Tesla can build left and right hand drive versions, as well as the Model X, from the same production line, greatly increasing production efficiency. Cars are built simultaneously for delivery to the same parts of the world, further promoting delivery efficiency.
Michael caught sight of three Model X cars during his tour — one just the bare chassis, one a well used testing mule and one a recently completed production car. His tour guide told him only about 20 people within the factory have ever seen a completed Model X in final form and ready for delivery to a customer.
For more of Michael’s insights from his factory tour, check out the full 20 minute video. You are bound to find out something about the company and its cars you didn’t know before.
Elon Musk
President Donald Trump buys a Tesla at the White House – Here’s which model he chose
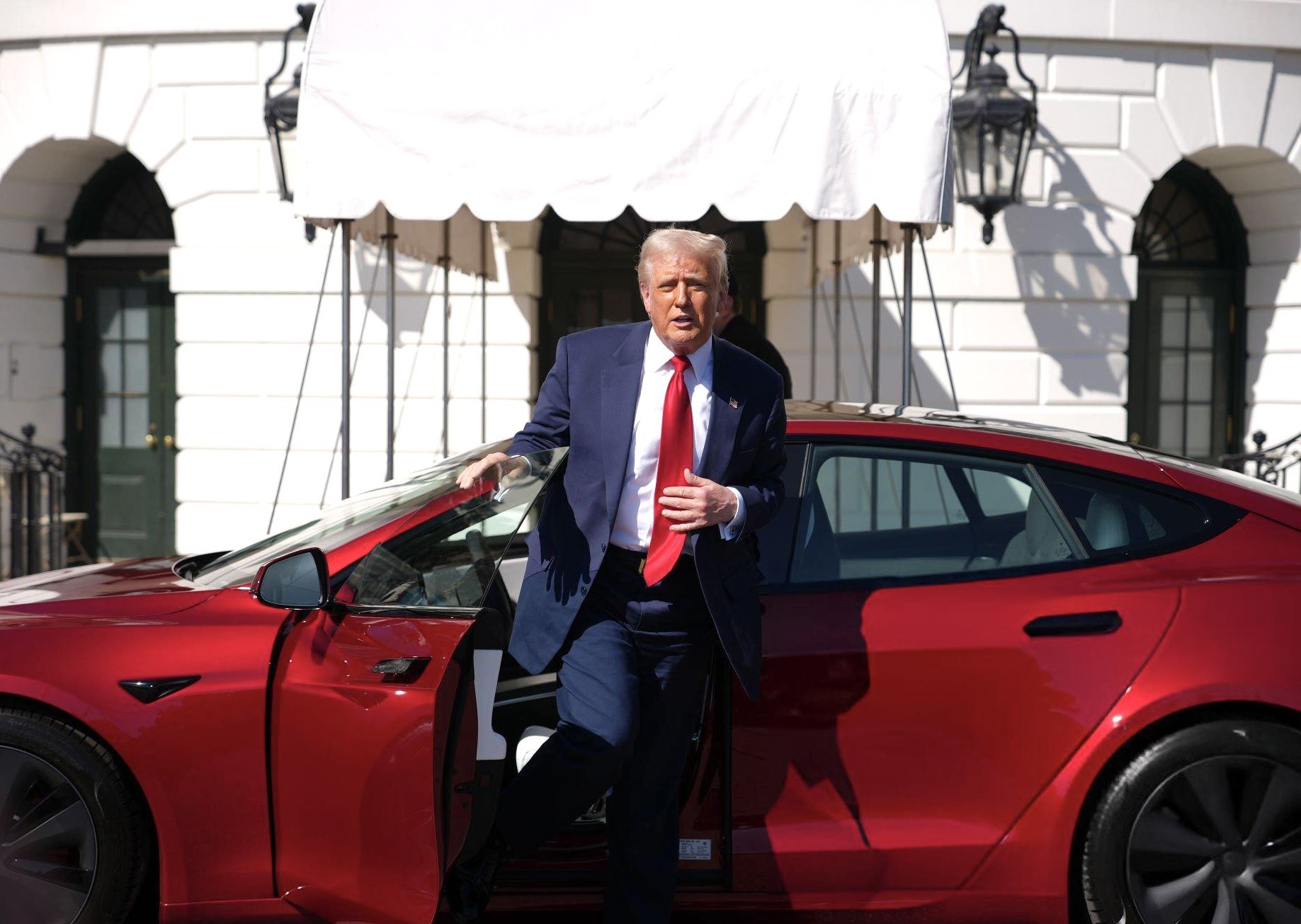
U.S. President Donald Trump was greeted by a convoy of Tesla electric vehicles today at the White House after he said last evening he would be buying one of the company’s cars in support of Elon Musk.
A variety of Tesla EVs, including the Model S, Cybertruck, and Model Y, all arrived in Washington on Tuesday around lunch time where the President sat in, examined, and mulled over which car he would choose. White House Press Secretary Karoline Leavitt told reporters today that President Trump would be paying “full market price” for the vehicle.
CEO Elon Musk was alongside Trump to help make his decision:
Which Tesla did President Trump Choose?
After mulling the decision for several minutes, President Trump seemed to have gravitated toward the Tesla Model S Plaid in Deep Red, the company’s quickest and most luxurious offering, suitable for the leader of the U.S.
Trump said:
“The one I like is that one (Model S). And I want that same color. I’m going to give [Tesla] a check. I don’t want a discount.”
According to images shared from Washington, it seems Musk brought two Model S vehicles — one in Deep Red and another in Deep Blue Metallic — knowing that the President would probably choose that vehicle, but was unsure about the color.
Tesla makes a decision on the future of its flagship Model S and Model X
President Trump’s Comments on Tesla and Elon Musk
President Trump has truly gained a meaningful working relationship with Musk, who he has called “a genius” and “brilliant” on several occasions. Regarding Tesla, the President said:
“Tesla’s a great company; They’re American cars, it’s American made. He employs thousands of people. He has the most modern plants in the world.”
In regards to the Tesla lineup, President Trump said:
“I know people that have these cars; It blows them away. They love them.”
When talking about the polarizing design of the Cybertruck, he said:
“In terms of imagination, and I think I have a pretty great imagination, who else but this guy would design this and everybody on the road is looking at it. As soon as I saw it, I said, ‘That’s the coolest design.’ You gotta give him (Elon) credit.”
News
Tesla makes a decision on the future of its flagship Model S and Model X
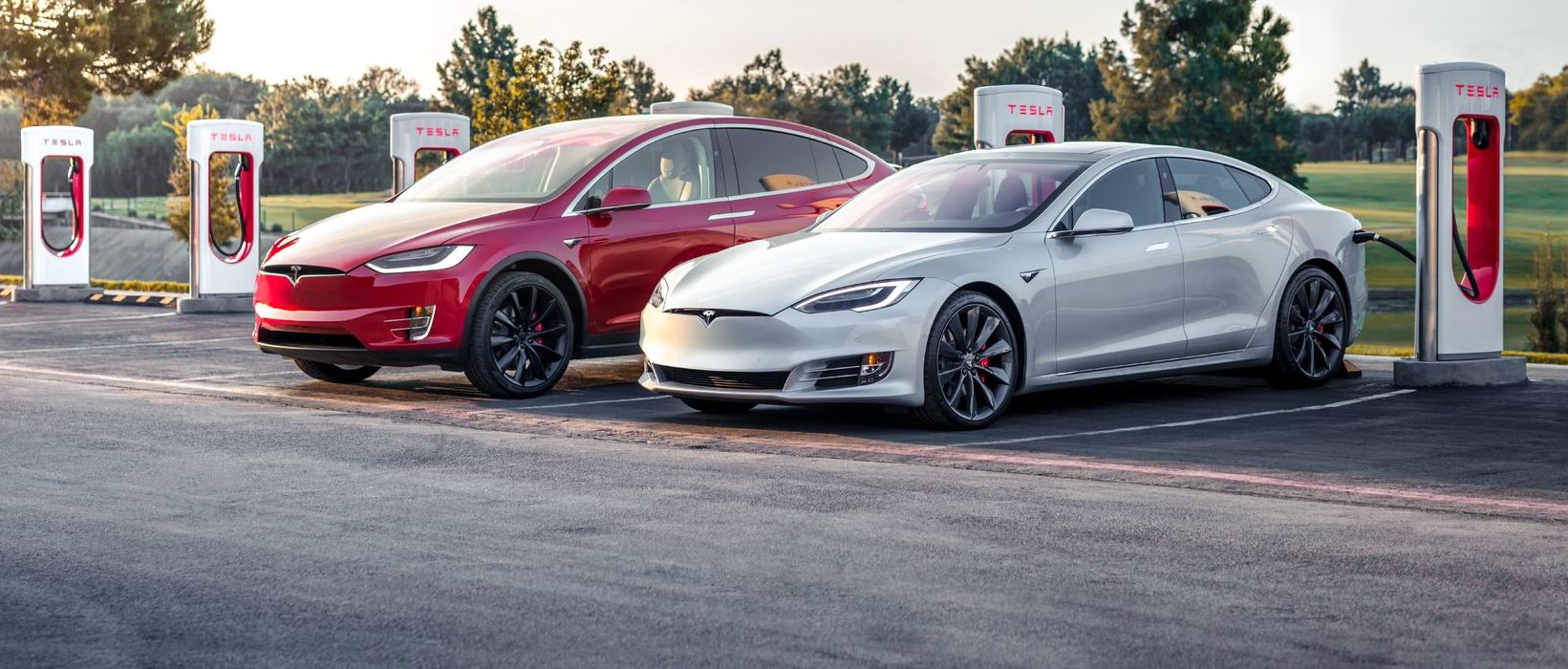
Tesla has made a decision regarding the future of its flagship vehicles, the Model S and Model X, which both have been sticking around for “sentimental reasons” and have no true alignment with the company’s future goals of growth.
The Model S and Model X were Tesla’s first two vehicles to be offered to the public.
They were essentially fundraisers for future, mass-market, affordable models, according to Elon Musk’s “Tesla Master Plan,” but their ability to still attract some buyers thanks to the performance of the Model S or the space of the Model X keeps them lingering.
But speculation regarding the vehicles’ true place in the expanding Tesla lineup has been persistent. With the vehicles, which have been grouped in with the Cybertruck in its quarterly delivery releases, only amounting to 23,000 deliveries in Q4, there are questions as to whether it is still worth keeping them around.
Tesla’s VP of Vehicle Engineering, Lars Moravy, said on the Ride the Lightning podcast yesterday that there are currently no plans to eliminate the Model S and Model X from the lineup.
When asked about whether there were plans for the Model S and Model X moving forward, Moravy replied:
“Just give it a minute. We’ll get there. The upgrade a couple of years ago was bigger than most people thought in terms of architecture and structure of the car got a lot better, too. But, we’ll give it some love later this year and make sure it gets a little bit…you know, with the stuff we’ve been putting in 3 and Y. Obviously, with 3 and Y, the higher volume stuff, you’ve gotta focus there.”
He confirmed that the two vehicles were not going anywhere “anytime soon.”
? When @DMC_Ryan asked Lars Moravy if Model S and Model X have some updates coming, the Tesla VP of Vehicle Engineering said:
“Just give it a minute. We’ll get there.”
Sounds like another refresh is coming, and the flagships aren’t going anywhere. pic.twitter.com/Y6MPp47MJC
— TESLARATI (@Teslarati) February 23, 2025
Moravy said the Model S and Model X are great consider when you consider autonomy and the robotaxi use: the Model S due to its overall quality and the Model X because of its interior space.
Need accessories for your Tesla? Check out the Teslarati Marketplace:
- https://shop.teslarati.com/collections/tesla-cybertruck-accessories
- https://shop.teslarati.com/collections/tesla-model-y-accessories
- https://shop.teslarati.com/collections/tesla-model-3-accessories
Please email me with questions and comments at joey@teslarati.com. I’d love to chat! You can also reach me on Twitter @KlenderJoey, or if you have news tips, you can email us at tips@teslarati.com.
News
Tesla is offering a crazy Supercharging incentive on its two ‘sentimental’ vehicles
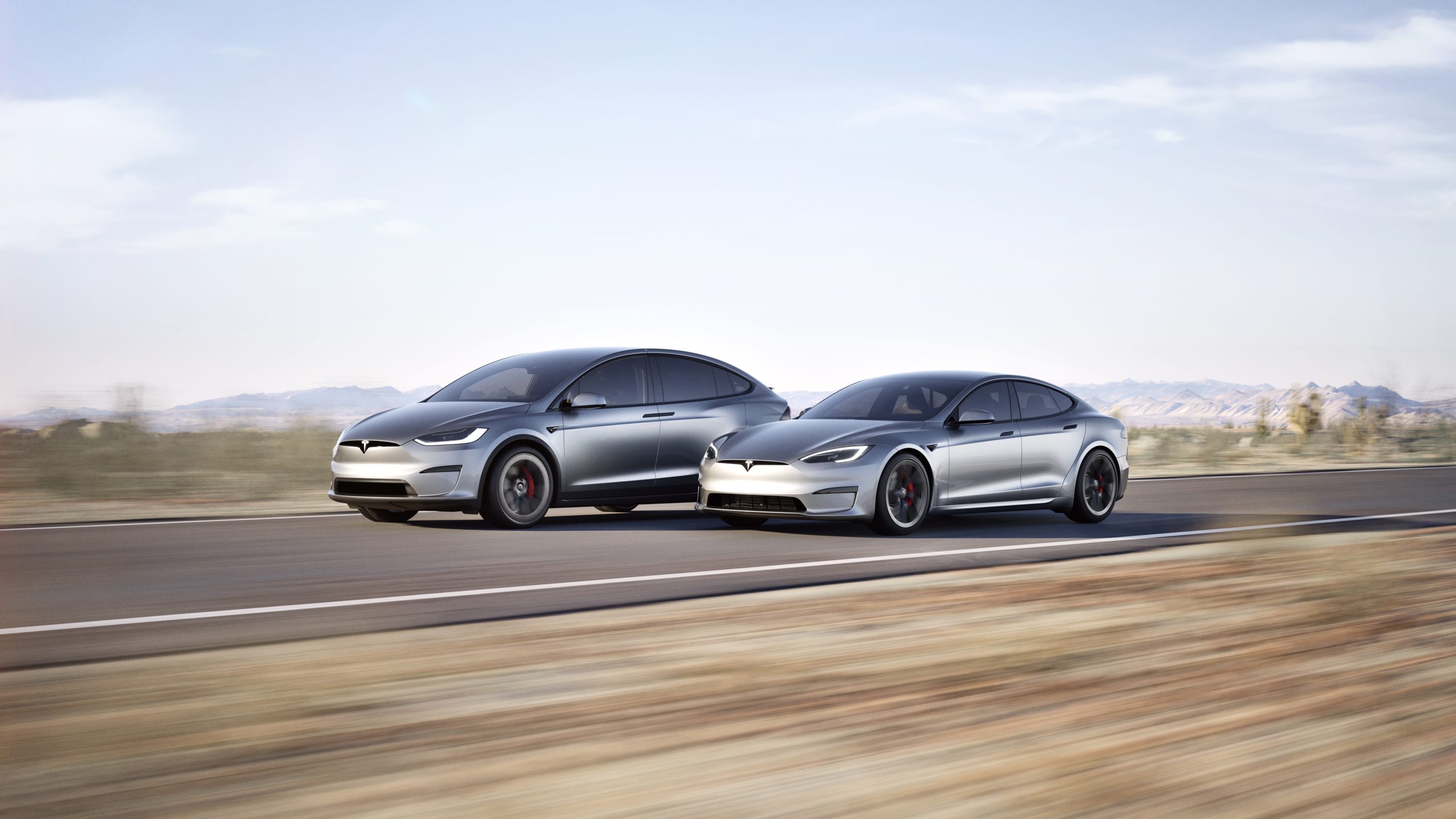
Tesla is offering a crazy Supercharging incentive for those who choose to buy two vehicles that CEO Elon Musk said the company is keeping around for “sentimental reasons” a few years ago.
Tesla Supercharging incentives are pretty hard to come by, and it is hard to tell when the company is going to offer them. Usually, they are used to move vehicles and nudge consumers toward purchasing one model over another.
However, Tesla sometimes offers Supercharging incentives at random times for no real reason other than luck of the draw.
However, Tesla is using the Supercharging incentive to help move two of the cars that are low-volume sellers, but are kept around for what Musk called “sentimental reasons” in 2019.
Tesla is offering free Supercharging for those who choose to purchase or lease a new Model S or Model X.
The offer is good for the life of your ownership or lease. Tesla talks more about the terms on its website:
“Customers who purchase or lease a new Model X (or Model S) are eligible for free Supercharging during your ownership of the vehicle. Offer is tied to your Tesla Account and cannot be transferred to another vehicle, person or order, even in the case of ownership transfer. Used vehicles, business orders and vehicles used for commercial purposes (like taxi, rideshare and delivery services) are excluded from this promotion. You are still responsible for Supercharger fees, like idle and congestion fees, when applicable.”
This is a great promotion to attempt and move some of Tesla’s vehicles, especially two that the company only keeps around because they are two of the company’s foundational, flagship cars.
Musk said in 2019:
“I mean, they’re very expensive, made in low volume. To be totally frank, we’re continuing to make them more for sentimental reasons than anything else. They’re really of minor importance to the future.”
Tesla has not released a major update to the Model S or Model X in a few years. In 2022, it launched the Plaid configuration, but it has not received any true modifications since then, leading some to believe they could be sunsetted in the future.
For now, it seems they will be sticking around, but Tesla is still adjusting the prices and incentives of the two vehicles. Earlier this week, Tesla pushed the Model X’s price in the U.S. up by $5,000.
Need accessories for your Tesla? Check out the Teslarati Marketplace:
- https://shop.teslarati.com/collections/tesla-cybertruck-accessories
- https://shop.teslarati.com/collections/tesla-model-y-accessories
- https://shop.teslarati.com/collections/tesla-model-3-accessories
Please email me with questions and comments at joey@teslarati.com. I’d love to chat! You can also reach me on Twitter @KlenderJoey, or if you have news tips, you can email us at tips@teslarati.com.
-
News6 days ago
Tesla rolls out new, more affordable trim of the Model Y Juniper in U.S.
-
News1 week ago
Tesla shares Optimus’ improved walk in new update video
-
Elon Musk2 weeks ago
Tesla vandal who lit Las Vegas repair center on fire arrested
-
Elon Musk2 weeks ago
Elon Musk clarifies Trump tariff effect on Tesla: “The cost impact is not trivial”
-
News2 weeks ago
Tesla US Gigafactories shields from Trump’s 25% Tariffs
-
Elon Musk2 weeks ago
Musk says xAI has acquired X in $33 billion stock deal
-
Elon Musk1 week ago
Tesla Germany reports 4,935 units sold in Q1 2025
-
Elon Musk2 weeks ago
Tesla vehicles hit by ATV, suspect caught by Sentry Mode