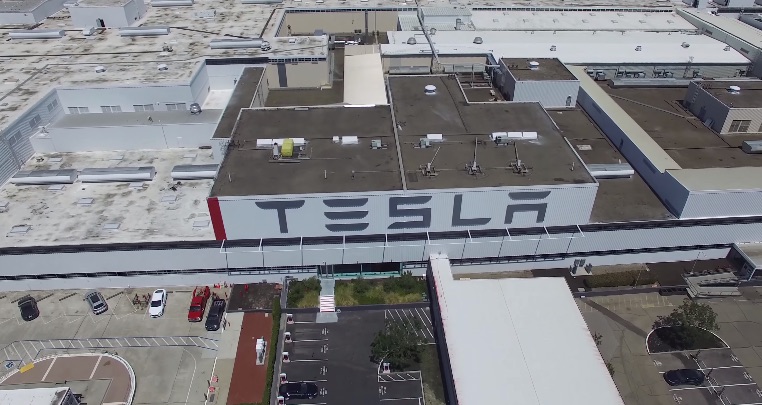
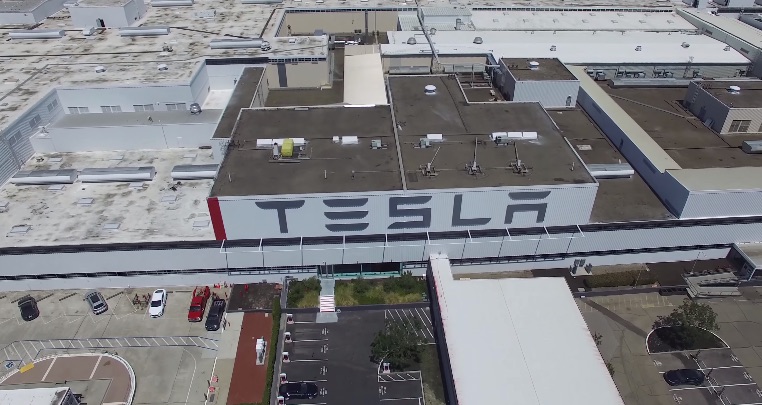
News
Tesla emphasizes factory safety, preempts possible smear campaign by auto union
Tesla released a blog post Sunday evening that reemphasizes the company’s goal to become the safest auto factory in the world. The post comes after the United Auto Workers Union (UAW) attempted to rally support earlier this year from Fremont factory workers in favor of unionizing.
Tesla states that it has received several media inquiries over allegations about safety at its Fremont, California factory. The well-timed nature of the inquiries, and similarity in topic, led Tesla to believe that the UAW was spreading anti-Tesla propaganda to the media in an attempt to provoke a response from the public, and from Tesla employees. In typical fashion, Tesla acted quickly and took to the offensive to defend the company’s approach to manufacturing, and maintaining the health and safety of its employees. The company has gone as far as forming dedicated Ergonomics Teams that have exclusive focus on “improving health and safety and reducing ergonomic risk for current and future production”.
“We are building entirely new vehicles from the ground up, using entirely new technology, production, and manufacturing methods, and ramping them at high volume. Getting this right is extremely difficult, and we deeply appreciate the hard work that all our employees do to help us achieve what most regard as impossible.” says Tesla through its blog post.
Tesla notes that in just 15 years, the company has become the largest manufacturing employer in California with over 10,000 production jobs in the Fremont factory and surrounding Bay Area.
Tesla has a proven track record of putting safety first as made evident by the award-winning safety ratings for its Model S and Model X. Vehicles have taken the brunt of the impact for their occupants, have swerved to avoid accidents and have even accelerated to avoid accidents. The innovative safety features Tesla has built into its vehicles is unsurpassed in the automotive world.
Though Tesla’s safety record to date is already better than industry-average, according to its press release, the company indicates that it continues to learn and apply new production processes aimed at improving employee well-being. Among the improvements are:
- Added 3rd shift to the manufacturing schedule to cut overtime because the employees asked for it and it was the right thing to do.
- Hired dedicated Ergonomist and established an Ergonomics team to ensure that current and future Tesla manufacturing lines are ergonomically friendly for employees.
- Model 3 has been designed with manufacturing employee ergonomics in mind. The Tesla Ergonomics Team works closely with design and engineering teams to catch ergonomics issues before they happen and proactively drive these improvements back into the design of the equipment and the car. Yes, you heard that right. Tesla will redesign the car if it is resulting in ergonomically challenging situations for its manufacturing employees.
- Established safety teams in every department which meets regularly to ensure safety is a top focus in its manufacturing operating departments.
These changes are not just skin deep and the company is seeing the results of the changes already. Tesla says it has collectively reduced 52% in lost time incidents and a 30% reduction in recordable incidents in the first quarter of 2017 versus the same period last year. These more granular metrics support an improvement in the industry standard Total Recordable Incident Rate (TRIR) which at the end of Q1 2017 was 4.6, a full 32% better than the industry standard of 6.7.
Anyone who has worked in an industry where safety is important can tell you that a culture of safety awareness is built day by day, month by month over many years. Tesla has a demonstrated history of superior results. The steps it has outlined to drive further improvements at the factory are evidence of a continued focus on safety and its employees.
The full post from the Tesla Blog reads as follows:
Creating the Safest Car Factory in the World
Earlier this year, the United Automobile Workers (UAW) announced it was attempting to organize workers in Tesla’s Fremont factory. The latest phase of their campaign involves a concerted and professional media push intended to raise questions about safety at Tesla.
We have received calls from multiple journalists at different publications, all around the same time, with similar allegations from seemingly similar sources about safety in the Tesla factory. Safety is an issue the UAW frequently raises in campaigns it runs against companies, and a topic its organizers have been promoting on social media about Tesla.
Some of the publications who have contacted us have rejected covering this “story” because they understand it is a misleading narrative based on anecdotes, not facts. However, there will likely be a few publications that choose to publish stories regardless, so we want to make sure the public also has the facts. Watch for these articles to downplay or ignore our actual 2017 safety data and to instead focus on a small number of complaints and anecdotes that are not representative of what is actually occurring in our factory of over 10,000 workers.
First, some context is important. The difficulty of starting a successful U.S. car company cannot be overstated, as evidenced by the fact that Ford is the only other U.S. car company to have never gone bankrupt. We are attempting to break this trend in order to fulfill our mission of accelerating the world’s transition to sustainable energy.
We are building entirely new vehicles from the ground up, using entirely new technology, production, and manufacturing methods, and ramping them at high volume. Getting this right is extremely difficult, and we deeply appreciate the hard work that all our employees do to help us achieve what most regard as impossible. While we still have a long way to go, in less than 15 years, we have become California’s largest manufacturing employer, creating more than 10,000 high-quality production jobs in the Bay Area, many of which had previously disappeared with the closure of NUMMI under the stewardship of the UAW.
As we work to achieve our mission, nothing is more important to us than protecting the health and safety of our employees. As we look at our safety record in prior years, we realize that we have not been perfect. No car factory is perfect, but particularly given that Model S and X were the first cars we built at more than tiny volumes, we fully acknowledge that they were not designed for ease of manufacturing – far from it. As would be expected, we have since learned many lessons, including how to improve the production process for the well-being of our colleagues.
Here are just some of the improvements that we have made:
- Historically, depending on production needs, some Tesla employees have worked significant amounts of overtime because it was necessary for the company to survive. However, working overtime can be challenging for employees and their families. Last year, we added a third shift to reduce the overtime burden on each team member and to improve safety. We did this because our employees asked for it, and because it was the right thing to do.
- As a result of this change, the average amount of hours worked by production team members has dropped to about 42 hours per week, and the level of overtime decreased by more than 60%. We hired our first dedicated Ergonomist in 2013, and in 2015 established an Ergonomics Team exclusively focused on improving health and safety and reducing ergonomic risk for current and future production.
- In addition to improving the process of building Model S and X, Model 3 has been designed specifically with ergonomics in mind. Our ergonomics team has worked hand-in-hand with our engineers on the design process. As just one example, we created simulations that showed us where reaching or bending by employees was most likely to occur, which in turn allowed us to redesign the equipment and the car to eliminate these issues as much as possible.
- Each department now has a Safety Team that meets regularly to increase safety awareness and recommend improvements, many of which have already been implemented.
- We are continuing to establish health and safety management procedures to scale with our operational growth.
The third shift, ergonomic improvements and increased safety awareness have collectively led to a 52% reduction in lost time incidents and a 30% reduction in recordable incidents from the first quarter of 2016 to the first quarter of 2017. In addition, through the end of Q1 2017, the factory’s total recordable incident rate (TRIR), the leading metric for workplace safety, is 4.6, which is 32% better than the industry average of 6.7. This data shows that there has been a dramatic improvement in employee safety, we are now significantly better than industry-average, and we continue to improve each day. A few anecdotes in a factory of over 10,000 people can always be given, but these are the facts.
Tesla’s safety record is much better than industry average, but it is not enough. Our goal is to have as close to zero injuries as humanly possible and to become the safest factory in the auto industry. We will get there by continuing to ask our employees to raise safety concerns and to keep proposing ideas that make things even better.
The alternative is to stop improving and to instead do what the rest of the industry, including the UAW, has always done. But being industry average would make our safety 32% worse. We care too much about our team to go backwards.
News
Tesla sales soar in Norway with new Model Y leading the charge
Tesla recorded a 54% year-over-year jump in new vehicle registrations in June.
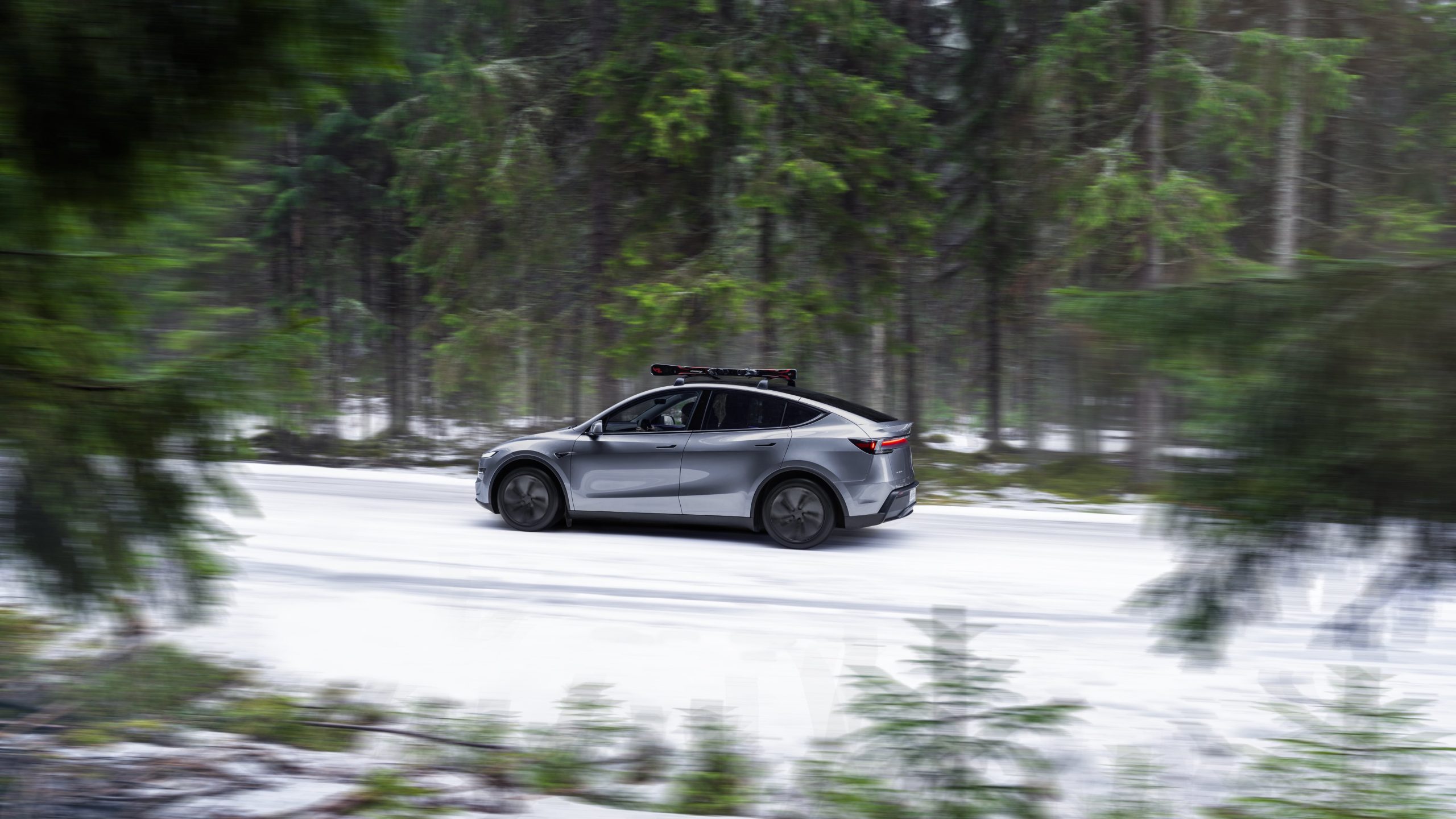
Tesla is seeing strong momentum in Norway, with sales of the new Model Y helping the company maintain dominance in one of the world’s most electric vehicle-friendly markets.
Model Y upgrades and consumer preferences
According to the Norwegian Road Federation (OFV), Tesla recorded a 54% year-over-year jump in new vehicle registrations in June. The Model Y led the charge, posting a 115% increase compared to the same period last year. Tesla Norway’s growth was even more notable in May, with sales surging a whopping 213%, as noted in a CNBC report.
Christina Bu, secretary general of the Norwegian EV Association (NEVA), stated that Tesla’s strong market performance was partly due to the updated Model Y, which is really just a good car, period.
“I think it just has to do with the fact that they deliver a car which has quite a lot of value for money and is what Norwegians need. What Norwegians need, a large luggage space, all wheel drive, and a tow hitch, high ground clearance as well. In addition, quite good digital solutions which people have gotten used to, and also a charging network,” she said.
Tesla in Europe
Tesla’s success in Norway is supported by long-standing government incentives for EV adoption, including exemptions from VAT, road toll discounts, and access to bus lanes. Public and home charging infrastructure is also widely available, making the EV ownership experience in the country very convenient.
Tesla’s performance in Europe is still a mixed bag, with markets like Germany and France still seeing declines in recent months. In areas such as Norway, Spain, and Portugal, however, Tesla’s new car registrations are rising. Spain’s sales rose 61% and Portugal’s sales rose 7% last month. This suggests that regional demand may be stabilizing or rebounding in pockets of Europe.
News
Tesla to open first India experience center in Mumbai on July 15
The event is scheduled for July 15 at the Bandra Kurla Complex, a premier business district in Mumbai.
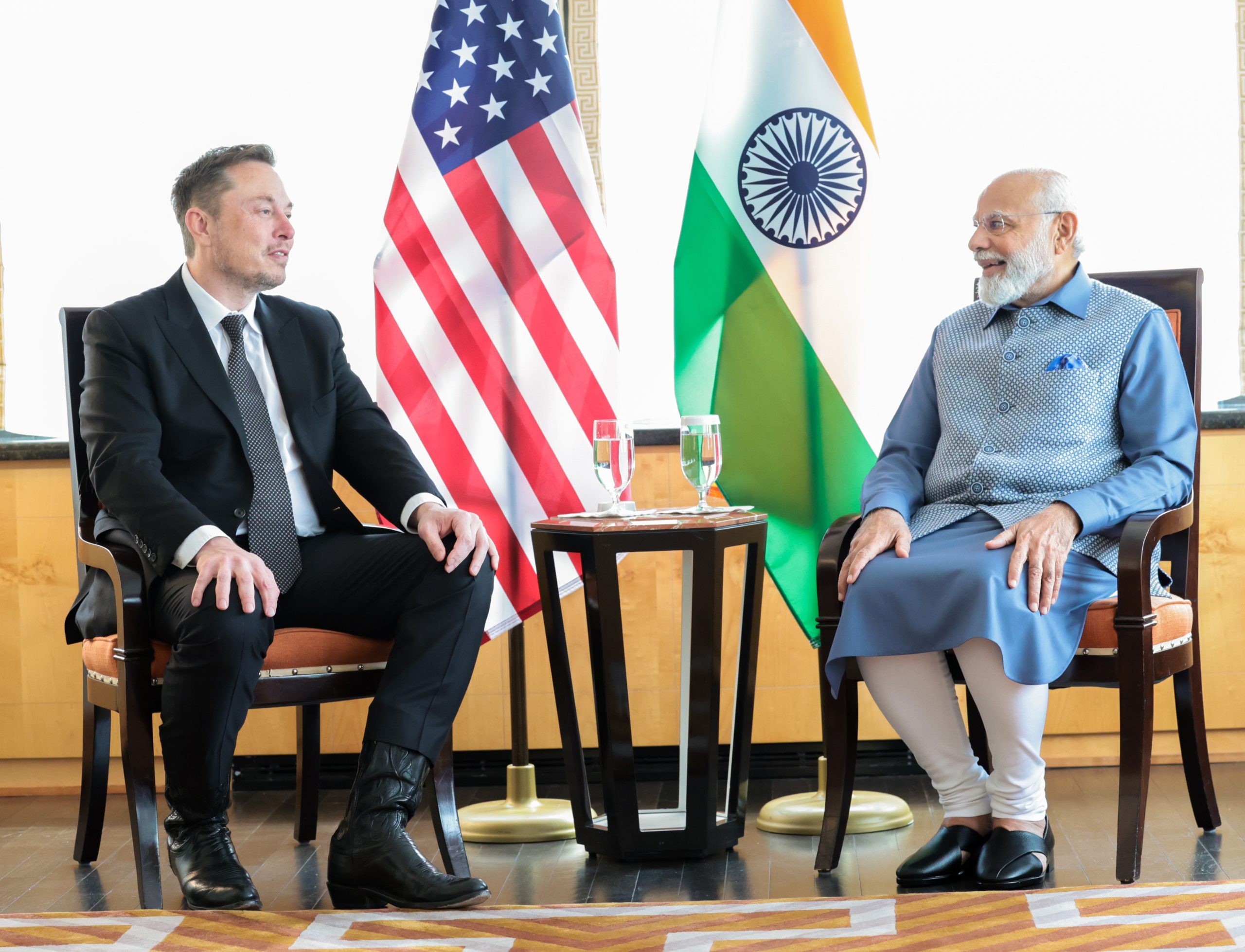
Tesla is officially entering India with the opening of its first showroom and experience center in Mumbai next week. The event is scheduled for July 15 at the Bandra Kurla Complex, a premier business district in Mumbai.
Tesla imports to India signal an early-stage market entry strategy
According to Indian customs data, Tesla has imported approximately $1 million worth of vehicles, charging equipment, and merchandise into the country between January and June. The shipments include six Model Y comprised of five standard variants valued at $32,500 each and one long-range model valued at $46,000. Several Superchargers and related accessories were also imported into the country, as noted in a Yahoo Finance report.
These vehicles are expected to serve as display models and test units as Tesla gauges interest and navigates India’s high import duties, which hover around 70% on fully built vehicles. Despite the significant tariffs in the country, Tesla has opted to begin its India expansion with imported cars.
An invitation to the Tesla India launch event has been making the rounds online. As could be seen in the document, Tesla noted that July 15 would be the launch of Tesla in India through the opening of a Tesla experience centre at Bandra Kurla Complex in Mumbai.
Tesla India’s hiring and expansion efforts are underway
Tesla has filled a number of key roles from the 30+ positions it advertised earlier this year. Recent hires include store managers, service executives, and sales staff, while ongoing recruitment is focused on supply chain engineers and vehicle operators to support the company’s Autopilot program.
Indian officials have been open about their intention to encourage Tesla to establish a manufacturing hub in the country. Tesla does seem open to the idea, at least, with reports last year hinting that Elon Musk was set to visit the country to discuss or even potentially announce a domestic project. The trip, however, was ultimately canceled.
News
Tesla begins Robotaxi certification push in Arizona: report
Tesla seems serious about expanding its Robotaxi service to several states in the coming months.
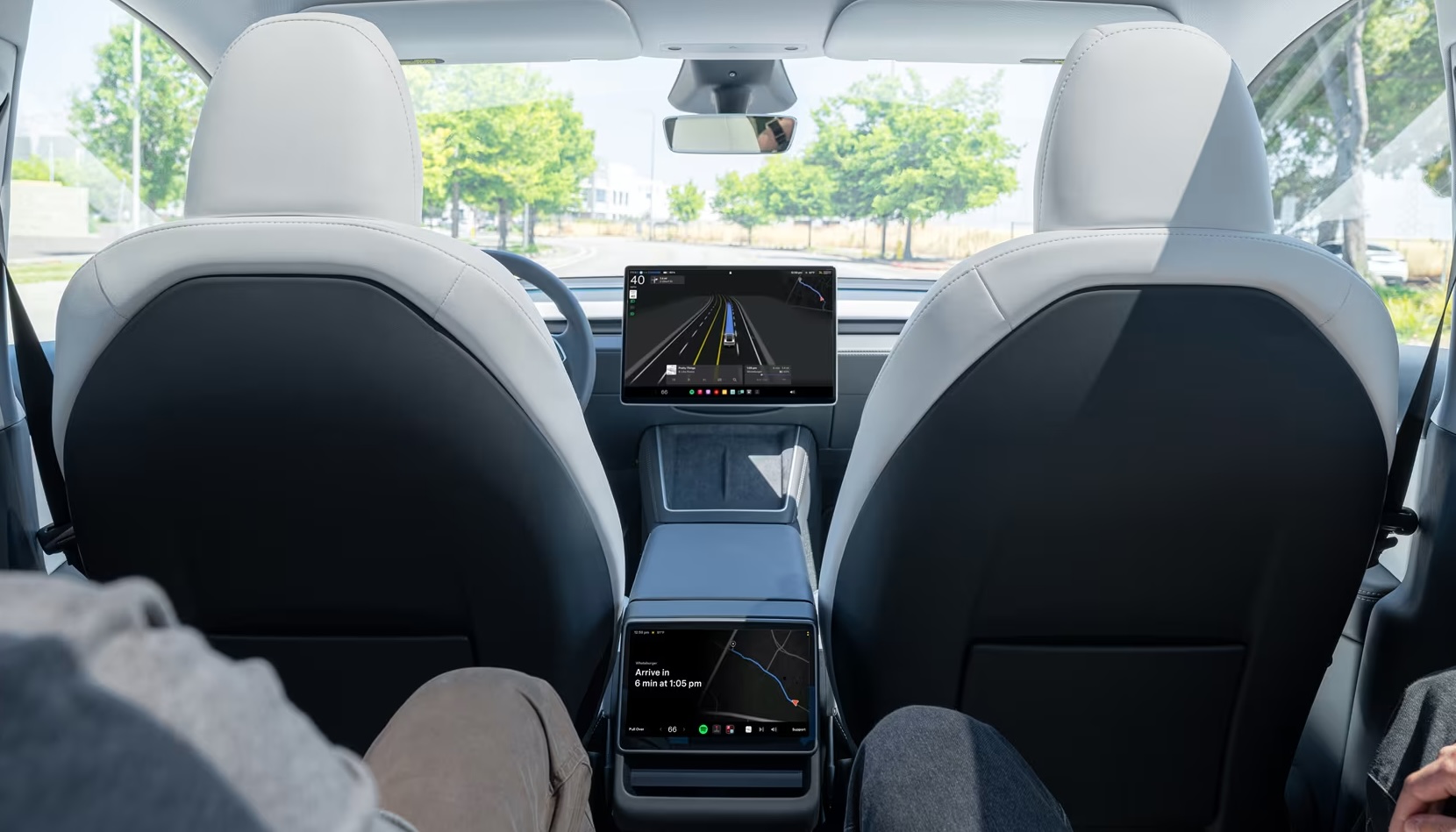
Tesla has initiated discussions with Arizona transportation regulators to certify its driverless Robotaxi service in the state, as per a recent report from Bloomberg News. The move follows Tesla’s launch of its Robotaxi pilot program in Austin, Texas, as well as CEO Elon Musk’s recent comments about the service’s expansion in the Bay Area.
The Arizona Department of Transportation confirmed to Bloomberg that Tesla has reached out to begin the certification process for autonomous ride-sharing operations in the state. While details remain limited, the outreach suggests that Tesla is serious about expanding its driverless Robotaxi service to several territories in the coming months.
The Arizona development comes as Tesla prepares to expand its service area in Austin this weekend, as per CEO Elon Musk in a post on X. Musk also stated that Tesla is targeting the San Francisco Bay Area as its next major market, with a potential launch “in a month or two,” pending regulatory approvals.
Tesla first launched its autonomous ride-hailing program on June 22 in Austin with a small fleet of Model Y vehicles, accompanied by a Tesla employee in the passenger seat to monitor safety. While still classified as a test, Musk has said the program will expand to about 1,000 vehicles in the coming months. Tesla will later upgrade its Robotaxi fleet with the Cyercab, a two-seater that is designed without a steering wheel.
Sightings of Cybercab castings around the Giga Texas complex suggests that Tesla may be ramping the initial trial production of the self-driving two-seater. Tesla, for its part, has noted in the past that volume production of the Cybercab is expected to start sometime next year.
In California, Tesla has already applied for a transportation charter-party carrier permit from the state’s Public Utilities Commission. The company is reportedly taking a phased approach to operating in California, with the Robotaxi service starting with pre-arranged rides for employees in vehicles with safety drivers.
-
Elon Musk2 weeks ago
Tesla investors will be shocked by Jim Cramer’s latest assessment
-
Elon Musk1 day ago
xAI launches Grok 4 with new $300/month SuperGrok Heavy subscription
-
Elon Musk4 days ago
Elon Musk confirms Grok 4 launch on July 9 with livestream event
-
News1 week ago
Tesla Model 3 ranks as the safest new car in Europe for 2025, per Euro NCAP tests
-
Elon Musk2 weeks ago
A Tesla just delivered itself to a customer autonomously, Elon Musk confirms
-
Elon Musk1 week ago
xAI’s Memphis data center receives air permit despite community criticism
-
News2 weeks ago
Xiaomi CEO congratulates Tesla on first FSD delivery: “We have to continue learning!”
-
News2 weeks ago
Tesla sees explosive sales growth in UK, Spain, and Netherlands in June